Aluminum Free Deodorants: Elevate Daily Confidence
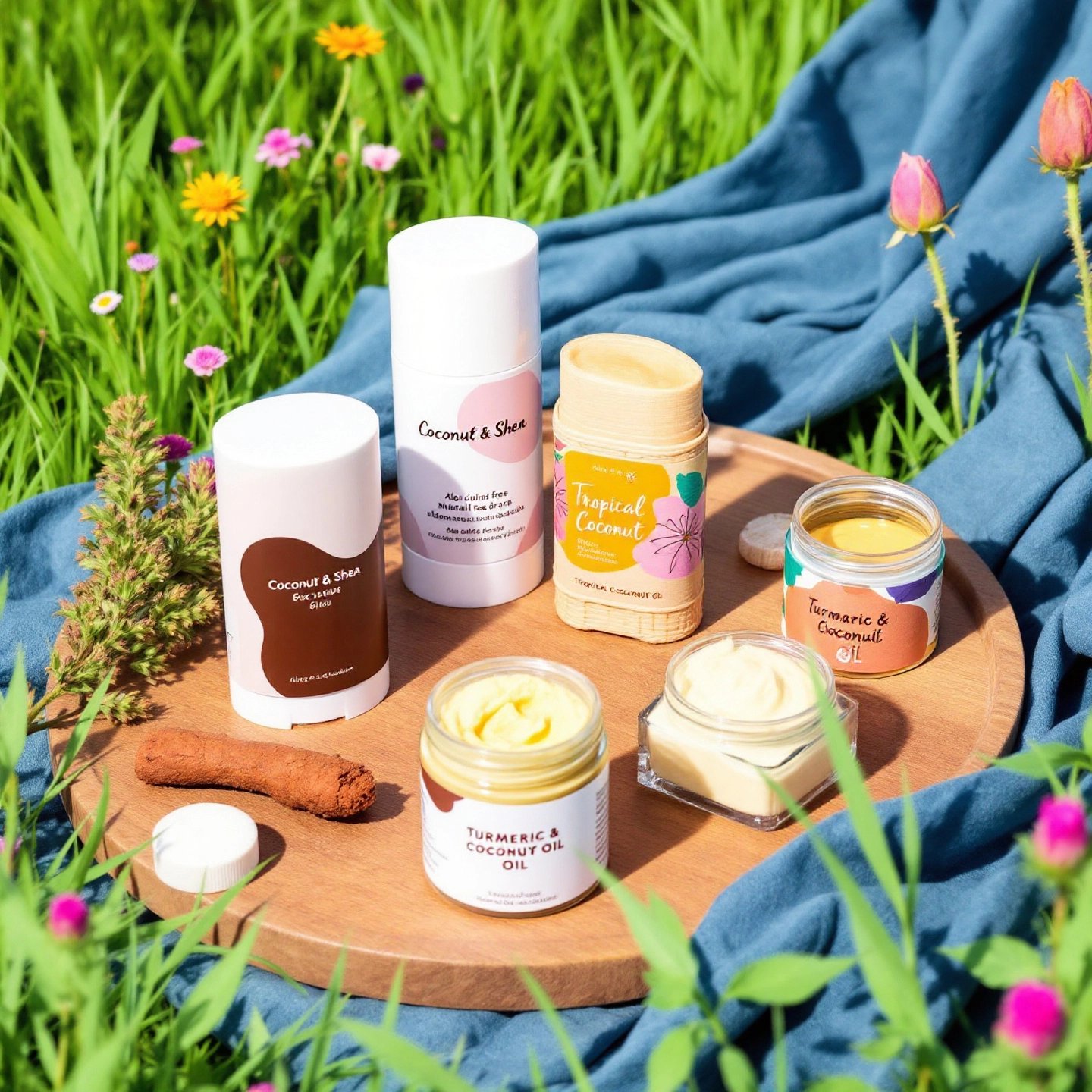
Introduction to Aluminum Free Deodorants
In recent years, the demand for aluminum free deodorants has surged, driven by a growing awareness of health and wellness trends in personal care. As consumers become more conscious of the ingredients in their skincare products, many are opting for natural alternatives that promise safer, gentler care for their skin. Aluminum free deodorants, in particular, have gained popularity because they avoid the use of aluminum compounds that are commonly found in traditional antiperspirants.
Unlike antiperspirants, which use aluminum to block sweat ducts and reduce perspiration, aluminum free deodorants focus on neutralizing odor without interfering with the body's natural sweating process. This shift aligns with the broader movement towards natural and sustainable personal care products, as highlighted in the 2025 Wellness in Beauty and Personal Care Trends Report, which emphasizes sustainability and wellness as key industry drivers.
Throughout this article, we will explore the benefits of choosing aluminum free deodorants, delve into the differences between deodorants and antiperspirants, and provide guidance on selecting the best products for individual needs. By understanding these aspects, you can make informed decisions about your personal care routine, ensuring it aligns with both your health goals and environmental values.
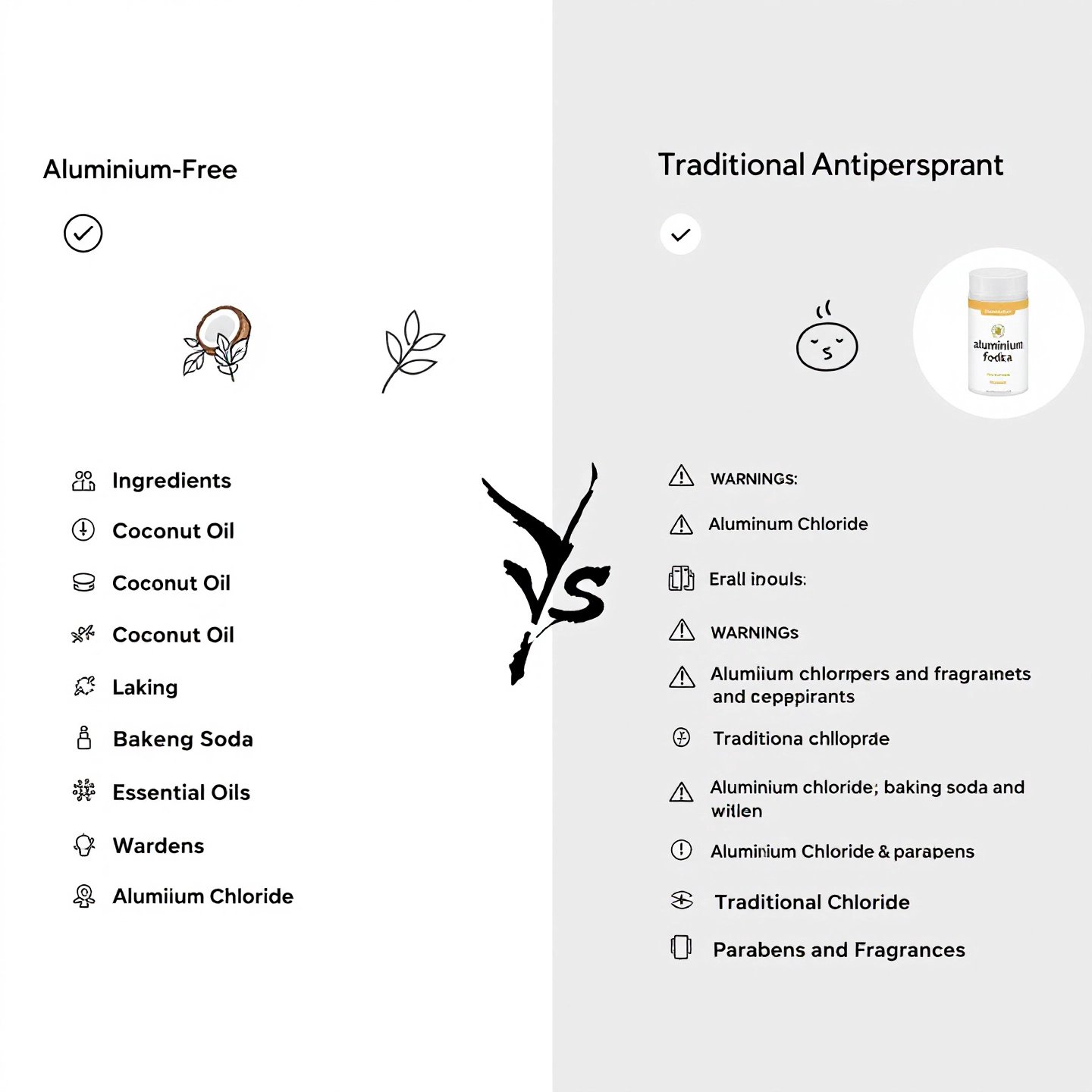
Unraveling The Basics Of Aluminum Free Options
When it comes to personal hygiene, understanding the difference between aluminum free deodorants and traditional antiperspirants is crucial. But what is aluminum free deodorant, and how does it differ from its aluminum-containing counterparts? Let's break it down.
Traditional antiperspirants use aluminum compounds to temporarily block sweat ducts, reducing perspiration. In contrast, deodorants that are aluminum free focus on neutralizing odor without affecting the body's natural sweating process. This distinction is important because while sweating is a natural body function, many prefer to manage odor without hindering sweat.
Deodorants vs. Antiperspirants
Deodorants and antiperspirants serve different purposes:
- Deodorants: Primarily aim to mask or neutralize body odor caused by bacterial growth in sweat. They often contain antimicrobial agents and fragrances to achieve this.
- Antiperspirants: Designed to reduce sweating by blocking sweat glands with aluminum-based compounds, thereby also reducing odor indirectly.
Understanding these differences helps you choose the right product based on your needs and preferences.
Common Ingredients in Aluminum Free Deodorants
Aluminum free deodorants often include a variety of natural ingredients:
- Powders and Starches: Corn starch or arrowroot powder to absorb moisture.
- Soothing Agents: Aloe vera and coconut oil for skin soothing and moisturizing properties.
- Antibacterial Ingredients: Tea tree oil and ethylhexylglycerin, which combat odor-causing bacteria.
- Fragrances: Essential oils like lemongrass or rosemary, providing a pleasant scent and additional antibacterial benefits.
Here's a brief comparison to highlight the key differences:
Feature |
Aluminum Free Deodorant |
Traditional Antiperspirant |
Primary Function |
Neutralizes odor |
Reduces sweating |
Main Ingredient |
Natural antimicrobials |
Aluminum compounds |
Effect on Sweating |
Allows natural sweating |
Blocks sweat glands |
By choosing aluminum free options, you can embrace a more natural approach to personal care, aligning with both health and environmental values. Next, we'll explore the health and environmental benefits these products offer, helping you make an even more informed choice.
Recognizing The Health And Environmental Benefits
Switching to aluminum free deodorants offers several compelling benefits for both your health and the environment. By understanding these advantages, you can make a more informed decision about your personal care products.
Health Benefits
- Reduced Skin Irritation: Many users find that aluminum free deodorants are gentler on the skin, reducing the risk of irritation, redness, and itching often associated with aluminum-based products.
- Natural Ingredients: These deodorants typically include natural components like coconut oil and shea butter, which not only combat odor but also nourish and moisturize the skin.
- Preservation of Natural Body Functions: Unlike antiperspirants, aluminum free options allow your body to sweat naturally, aiding in temperature regulation and toxin expulsion.
Environmental Benefits
- Reduced Chemical Pollution: By avoiding aluminum and other harsh chemicals, these deodorants minimize the risk of contaminating water systems, thus protecting aquatic life and ecosystems.
- Sustainable Packaging: Many brands focus on eco-friendly packaging, reducing plastic waste. This aligns with broader environmental goals and supports a more sustainable lifestyle.
Here's a quick comparison to illustrate these benefits:
Aspect |
Aluminum Free Deodorant |
Traditional Deodorant |
Skin Impact |
Gentle, reduces irritation |
Can cause irritation |
Environmental Impact |
Eco-friendly, less pollution |
Potentially harmful chemicals |
By choosing aluminum free deodorants, you're not only prioritizing your health but also making a positive impact on the environment. As we proceed, we'll delve into how these products cater to different needs, ensuring everyone can find their perfect match.
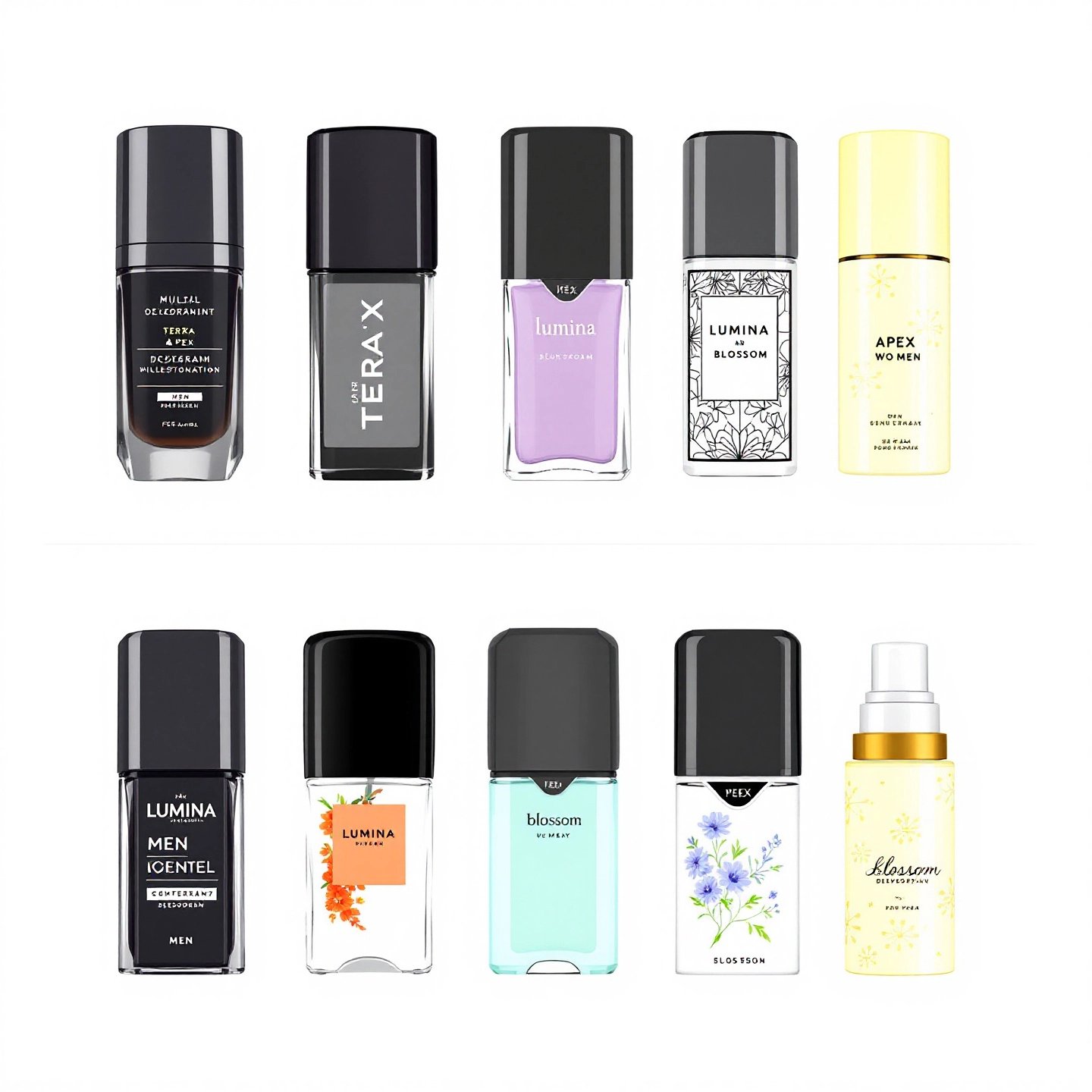
Choosing The Right Product For Men And Women
Selecting the ideal aluminum free deodorant often boils down to personal preferences, but there are notable differences between those marketed for men and women. These differences are primarily in scent profiles and formulation strengths, with each catering to perceived gender-specific needs.
Understanding Gender-Specific Needs
While both men and women can use any deodorant, manufacturers often differentiate products based on scent and packaging. Men's deodorants typically feature robust, musky, or fresh scents like sandalwood or citrus, while women's deodorants lean towards floral, fruity, and sweet aromas such as lavender or vanilla. This division, largely driven by cultural expectations, doesn't imply any real biological necessity, allowing for personal preference to guide choice.
Formulation strengths also vary, with men's products often marketed as providing "extreme protection" due to the higher average sweat levels in men. Women's versions might highlight "gentle care" with added moisturizers like aloe or shea butter, ideal for those with sensitive skin. However, these distinctions are more about marketing than actual ingredient differences, as most aluminum free options share similar compositions.
Key Considerations for Choosing Your Deodorant
- Sweat Level: Opt for stronger formulations if you perspire heavily, regardless of gender labeling.
- Skin Sensitivity: Choose products with soothing ingredients if you have sensitive skin.
- Fragrance Preference: Pick a scent you enjoy, whether traditionally masculine or feminine.
- Packaging Preferences: Consider eco-friendly options, such as those offered by brands like Sunmay Aluminum, which focus on sustainable packaging solutions.
Sunmay Aluminum, for instance, provides innovative packaging solutions that help deodorant brands meet consumer demands for sustainability. Their expertise in crafting high-quality aluminum profiles ensures that brands can offer eco-conscious packaging without compromising on aesthetic appeal or functionality.
Ultimately, the best aluminum free deodorant is one that aligns with your personal needs and lifestyle, offering both effectiveness and comfort. As you explore the options available, remember that the label doesn't define the product's suitability for you. Up next, we'll compare popular brands, helping you make informed choices based on unique features and price ranges.
Comparing Popular Brands And Their Unique Formulas
When choosing an aluminum free deodorant, understanding the offerings of major brands like Dove, Secret, and Arm & Hammer can guide you towards making a choice that best fits your needs. Each brand brings something unique to the table, whether it's in terms of scent, formulation, or price.
Dove Aluminum Free Deodorant
Dove's 0% Aluminum Deodorant is renowned for its moisturizing properties, making it an excellent choice for those with sensitive skin. It glides on smoothly and offers a wide range of scents, including the refreshing cucumber & green tea. Priced affordably around $6 at major retailers, it provides good value for money without compromising on quality. However, some users find the scents slightly synthetic, which might not appeal to everyone.
Secret Aluminum Free Deodorant
Secret offers a solid option with its Daylily scent, providing a clear, solid application. While it effectively masks odors, some users have noted a faint mildew scent upon warming on the skin, which might be a consideration for those sensitive to scents. Despite this, Secret remains a popular choice for its pleasant initial fragrance and effective odor control.
Arm & Hammer Essentials
Arm & Hammer utilizes the power of baking soda and natural plant extracts in its Essentials deodorant line. Known for its strong odor protection, it is a favorite among those who require more robust formulations. It is priced competitively, often found under $5, making it an attractive option for budget-conscious consumers.
Here's a comparison table to help you evaluate these brands:
Brand |
Key Features |
Price Range |
Dove |
Moisturizing, wide scent range |
$6 - $7 |
Secret |
Clear application, floral scents |
$5 - $8 |
Arm & Hammer |
Baking soda-based, strong odor control |
$4 - $6 |
Each of these brands offers distinct advantages, whether you prioritize skin sensitivity, scent preference, or budget. As you consider these options, remember that the best deodorant is one that aligns with your personal needs and lifestyle. Next, we'll delve into the differences between aluminum free antiperspirants and regular deodorants, helping you understand their roles in sweat management and odor control.
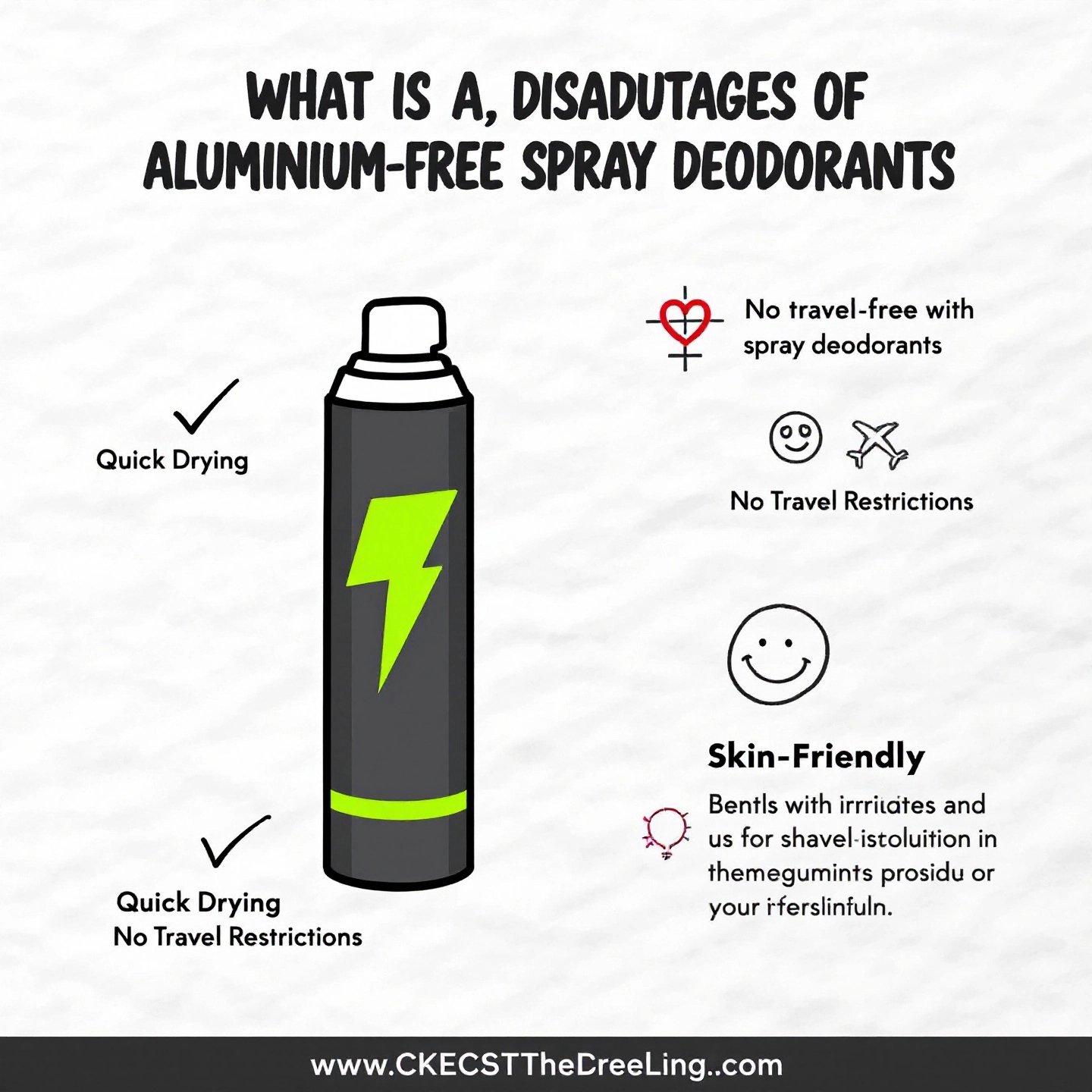
Understanding The Role Of Antiperspirants And Sprays
When navigating the world of personal care products, it's essential to understand the fundamental differences between aluminum free antiperspirant deodorant and regular deodorants. These products serve distinct purposes, primarily revolving around sweat management and odor control.
Aluminum Free Antiperspirants vs. Regular Deodorants
The primary distinction lies in their core functions:
- Aluminum Free Antiperspirants: Traditionally, antiperspirants are designed to reduce sweating by using aluminum compounds to block sweat glands. Aluminum free versions, however, focus on minimizing moisture through alternative ingredients, though they may not be as effective in completely halting sweat.
- Regular Deodorants: These products aim to neutralize body odor without affecting sweat production. They typically contain antibacterial agents and fragrances to mask or eliminate odors.
Choosing between these depends on your personal needs—whether you prioritize staying dry or simply want to manage odor.
Pros and Cons of Aluminum Free Spray Deodorants
Spray deodorants have become a popular choice for many, offering unique benefits and some drawbacks:
Pros:
- Instant Drying: Unlike stick or roll-on forms, spray deodorants dry quickly, allowing you to dress immediately without worrying about stains.
- Easy Layering: Reapplication is hassle-free, as the initial layer dries completely, preventing any sticky residue.
- Smooth Application: Sprays provide a non-sticky, smooth feel, avoiding the clumping sometimes associated with other forms.
Cons:
- Travel Restrictions: Spray cans must adhere to TSA regulations, making them less convenient for air travel compared to solid options.
- Potential Harshness: The aerosol fumes can be overwhelming and may irritate sensitive skin, especially if applied immediately after shaving.
- Temperature Sensitivity: The initial application can feel cold, which might be uncomfortable for some users.
Here's a quick comparison to help visualize these differences:
Feature |
Aluminum Free Antiperspirants |
Regular Deodorants |
Primary Function |
Minimizes moisture |
Neutralizes odor |
Main Ingredient |
Natural moisture absorbers |
Antimicrobial agents |
Effect on Sweating |
Reduces sweating |
Allows natural sweating |
Understanding these differences can help you select the most suitable product based on your lifestyle and preferences. Next, we'll address common concerns about the effectiveness of aluminum free deodorants and discuss how to optimize their use in your daily routine.
Evaluating Effectiveness And Common Concerns
When transitioning to aluminum free deodorants, many users have questions about their effectiveness and what to expect during the adaptation period. Understanding these aspects can help set realistic expectations and enhance your personal care routine.
Does Aluminum Free Deodorant Work?
Aluminum free deodorants are designed primarily to combat odor rather than prevent sweating. They work by using natural antibacterial agents to neutralize the bacteria that cause body odor. While they might not keep you as dry as traditional antiperspirants, they allow your body to sweat naturally, which is a healthy bodily function.
Whether or not they 'work' depends largely on your personal needs and lifestyle. For those who value natural ingredients and are less concerned about moisture, these deodorants can be an excellent choice. However, if you prioritize dryness, you might need to explore additional sweat management strategies.
Is Aluminum Free Deodorant Better?
The term 'better' is subjective and depends on what you prioritize in a deodorant. Here are some factors to consider:
- Health Benefits: Free from aluminum compounds, these deodorants are less likely to cause skin irritation and are often preferred by those with sensitive skin.
- Environmental Impact: Aluminum free options typically use eco-friendly packaging, aligning with sustainable practices.
- Natural Ingredients: Many contain soothing elements like coconut oil and shea butter, providing additional skin benefits.
Common Concerns and Adaptation Period
Switching to aluminum free deodorants can involve an adaptation period, during which your body adjusts to sweating more freely. Some users report increased odor or wetness initially, but this usually subsides as your body acclimates.
Here are some tips to ease the transition:
- Give your body time to adjust, typically a few weeks.
- Reapply deodorant throughout the day if needed, especially during the initial phase.
- Consider using a combination of deodorant and sweat-absorbing clothing to manage moisture.
Sunmay Aluminum's Role
Sunmay Aluminum plays a crucial role in enhancing product longevity and storage through their innovative packaging solutions. Their expertise in high-quality aluminum profiles ensures that deodorants are not only effective but also environmentally conscious, supporting brands in delivering sustainable products to consumers.
As you explore these options, remember that the best deodorant is one that aligns with your personal values and lifestyle needs. Up next, we'll showcase the best aluminum free deodorant picks for various specific needs, helping you find the perfect match for your routine.
Navigating Best Picks For Specific Needs
Choosing the right aluminum free deodorant can be daunting, given the multitude of options available. Whether you have sensitive skin or prefer fragrance-free alternatives, there are products tailored to meet your specific needs. Here's a curated list of top picks to help you make an informed choice.
Best Aluminum Free Deodorant for Sensitive Skin
- Bravo Sierra Unscented Deodorant: Ideal for sensitive skin, this deodorant is free from fragrances and baking soda, which are common irritants. It includes jojoba oil for added moisture, ensuring a gentle application.
- Native Sensitive Baking Soda-Free Deodorant: Known for its soothing formula, this option utilizes coconut oil and shea butter to prevent irritation while providing effective odor control.
Fragrance-Free Options
- Drunk Elephant Sweet Pitti Deodorant Cream: This cream deodorant uses mandelic acid to neutralize odor-causing bacteria, offering a fragrance-free solution that also helps fade hyperpigmentation.
- Attitude Plastic-Free Deodorant: Eco-conscious and gentle, this deodorant is both fragrance and essential oil-free, packaged in sustainable paper, making it a planet-friendly choice.
Additional Top Picks
- Lume Natural Deodorant: A versatile option suitable for the whole body, it uses mandelic acid to combat odor, making it perfect for those seeking comprehensive odor protection.
- Schmidt's Aluminum Free Natural Deodorant: This product stands out for its natural ingredients like shea butter and jojoba oil, providing long-lasting freshness without irritation.
By selecting a deodorant that aligns with your skin type and personal preferences, you can enhance your daily routine with confidence and comfort. As we proceed, we'll explore the importance of maintaining overall hygiene practices for optimal odor control.
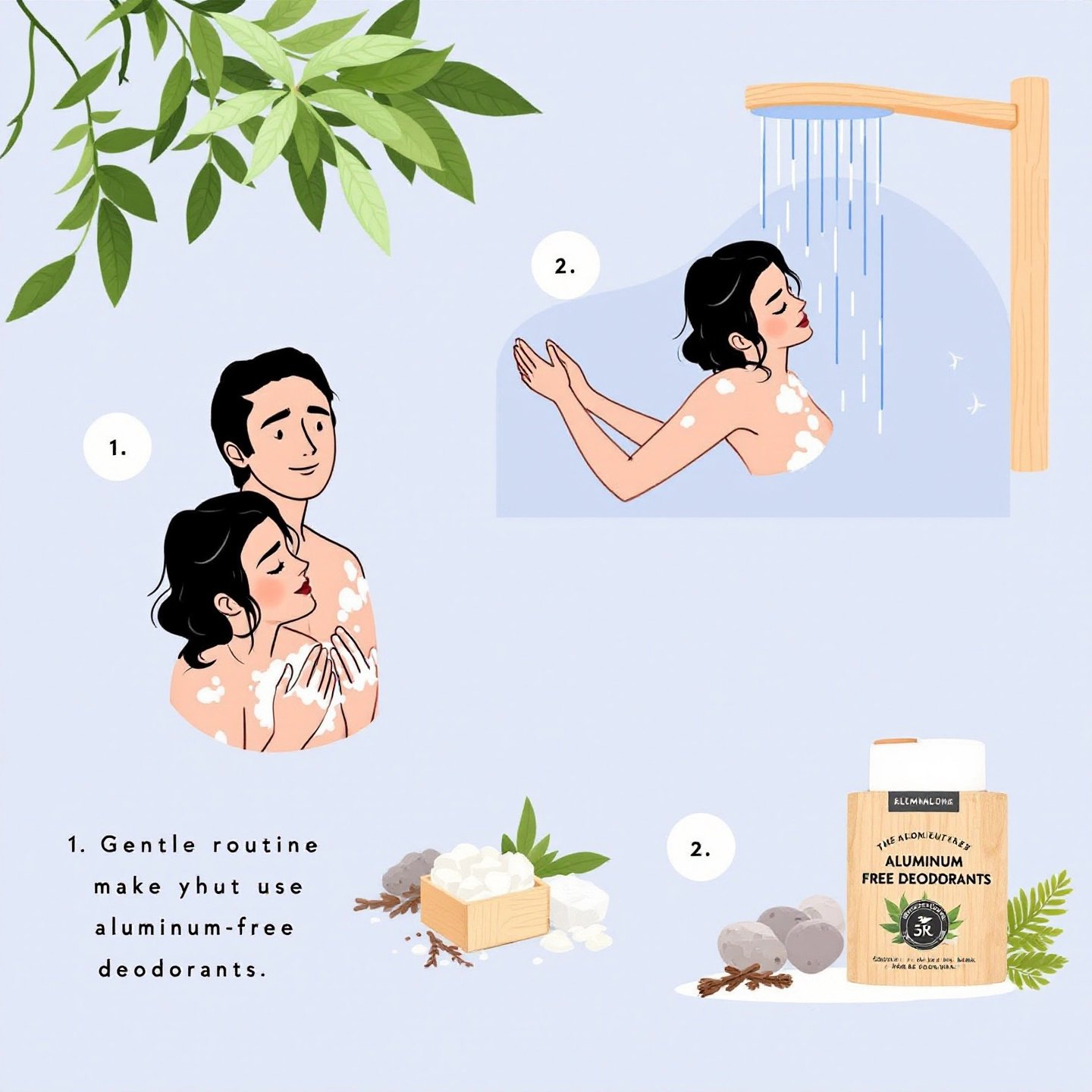
Building A Sustainable Routine For Ongoing Protection
Creating an effective aluminum free deodorant routine involves more than just picking the right product. It's about integrating it into a broader hygiene strategy that supports optimal odor control and skin health. Imagine starting your day with a refreshing shower, followed by the application of a deodorant that not only keeps you smelling fresh but also aligns with your personal values and skin needs.
To enhance the effectiveness of aluminum free deodorants, consider these key hygiene practices:
- Regular Showering: Consistent showering helps remove sweat and bacteria, which are primary contributors to body odor. Using a gentle, fragrance-free soap can prevent skin irritation while maintaining cleanliness.
- Proper Underarm Care: Keeping underarms dry and clean is crucial. After showering, ensure they are thoroughly dried before applying deodorant to maximize its effectiveness.
- Rotating Scents: To prevent skin irritation and olfactory fatigue, consider rotating between different deodorant scents. This not only keeps your routine interesting but also allows your skin to adapt to various formulations.
- Diet and Hydration: A balanced diet and adequate hydration can influence body odor. Foods rich in chlorophyll, such as leafy greens, can help reduce odor naturally.
By incorporating these practices into your daily routine, you'll notice a significant improvement in odor control and overall skin health. Moreover, these habits support the natural functions of your body while complementing the benefits of aluminum free deodorants. As we conclude our exploration of these products, we'll reflect on the future of personal care trends and how they continue to evolve.
Conclusion
As we've explored throughout this article, aluminum free deodorants offer a compelling blend of health benefits and environmental advantages, making them an appealing choice for the conscious consumer. By allowing the body to sweat naturally and using ingredients that are gentle on the skin, these products align with the growing demand for natural and sustainable personal care solutions.
Looking ahead, the future of aluminum free deodorants appears promising. With the market expected to expand significantly, driven by increased health awareness and a shift towards chemical-free products, we can anticipate more innovation in formulations and packaging. Brands are likely to introduce diverse options to cater to various skin types and preferences, further enhancing consumer choice.
In this evolving landscape, companies like Sunmay Aluminum play a pivotal role. By offering sustainable packaging solutions, they enable brands to meet consumer demands for eco-friendly products without compromising on quality or aesthetics. Sunmay Aluminum's expertise in crafting high-quality aluminum profiles ensures that deodorant brands can deliver products that are both effective and environmentally responsible.
Ultimately, choosing the right deodorant is a personal decision that should reflect your individual needs and values. As you navigate this journey, consider the broader impact of your choices on your health and the environment. Embrace the shift towards natural personal care, and explore the diverse offerings available to find a product that truly elevates your daily confidence.
Frequently Asked Questions about Aluminum Free Deodorants
1. Are deodorants without aluminum safe?
Yes, aluminum-free deodorants are considered safe as they primarily use natural ingredients to neutralize odor, reducing the risk of skin irritation compared to traditional antiperspirants.
2. What does aluminum free deodorant do for your body?
Aluminum-free deodorants help reduce armpit irritation and support the body's natural detoxification through sweating, using natural fragrances and moisturizers for healthier skin.
3. What is the healthiest deodorant to use?
The healthiest deodorants are those free from aluminum and harsh chemicals, often featuring natural ingredients like coconut oil and shea butter to maintain skin health.
4. Does aluminum free deodorant work?
Aluminum-free deodorants effectively neutralize odor using natural antibacterial agents, though they may not prevent sweating as traditional antiperspirants do.
5. Is aluminum free deodorant better?
Aluminum-free deodorants are better for those seeking natural ingredients and reduced skin irritation, aligning with eco-friendly and health-conscious lifestyles.