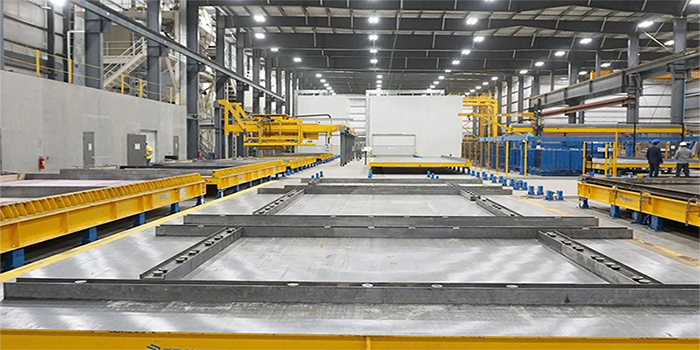
In the production process of precast concrete components, precision control has always been a key problem. Traditional formwork systems have many problems in terms of dimensional deviation, component consistency and rework rate. Especially in mass production, these problems will be further amplified, seriously affecting production efficiency and product quality. However, with the emergence of magnetic formwork systems, this situation has been significantly improved. With its unique design and function, the magnetic formwork system has brought unprecedented precision improvement to precast concrete production and has become the "new favorite" of the construction industry.
Precise positioning and dimensional deviation control
The Precast Concrete Formwork Magnet uses strong magnetic force to firmly fix the formwork on the prefabricated platform. This magnetic connection method can ensure that the formwork remains stable during the concrete pouring process and will not be displaced by external force or vibration. Compared with traditional bolt or welding fixing methods, the installation and removal of magnetic formwork is simpler and faster, and at the same time avoids dimensional deviation caused by loose installation or welding deformation. In actual operation, workers can quickly adjust the position and angle of the formwork according to the design requirements of the prefabricated components to achieve precise positioning, thereby effectively controlling the dimensional deviation of the components and enabling the dimensional accuracy of the prefabricated components to reach higher standards.
Improved component consistency
When mass-producing precast concrete components, it is crucial to maintain component consistency. The Precast Concrete Magnetic Formwork, through its modular design and standardized magnetic connection parts, can ensure that the formwork system of each precast component has the same structure and size. This means that during the production process, each component can be cast and formed under the same formwork conditions, which greatly improves the consistency of the components. In addition, the magnetic formwork system can also flexibly combine and adjust the formwork modules according to the different shapes and sizes of precast components, achieving diversified production while maintaining high quality consistency.
Reduce rework rate
Since the magnetic formwork system can effectively control dimensional deviations and improve component consistency, the component failure rate caused by formwork problems in precast concrete production has been greatly reduced. During the use of traditional formwork systems, problems such as formwork deformation and loose connections are prone to occur. These problems often lead to quality problems such as cracks and dimensional discrepancies in precast components, which require rework. The magnetic formwork system reduces the occurrence of these problems, reduces the rework rate, and improves production efficiency through its stable magnetic connection and precise positioning function. In mass production, this not only saves time and cost, but also improves the market competitiveness of enterprises.
Ideal for mass production
Magnetic formwork systems are particularly suitable for mass production of precast concrete components. In mass production, production efficiency and product quality stability are the two aspects that companies pay most attention to. The rapid installation and removal function of the magnetic formwork system can significantly shorten the replacement time of the formwork and improve production efficiency. At the same time, its high precision and high consistency can ensure that each precast component meets the quality standards, reducing production interruptions and rework caused by quality problems. In addition, the magnetic formwork system has a long service life and can be reused, which reduces the replacement cost of the formwork. These advantages make the magnetic formwork system extremely cost-effective in mass precast concrete production.