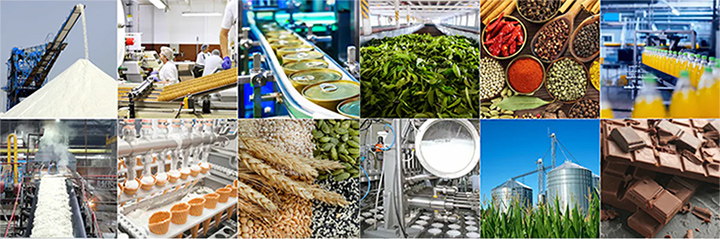
In a food processing plant that pursues deliciousness and health, you may not think of "magnets" at the first time. However, these invisible magnetic field forces are indispensable key players in ensuring the safety of our dining tables and improving production efficiency. They are unknown, but they have a great responsibility - they are specifically designed to deal with those "uninvited guests" that may be mixed into food: metal impurities.
* Wide range of sources: Metal impurities may come from raw materials (such as harvester parts fragments and ore residues in grain), production equipment (such as screen wear, loose and falling mechanical parts), employee negligence (such as screws, washers), and even packaging materials.
* Huge harm:
Physical damage: Sharp metal fragments are a major threat to consumer safety and may cause damage to the mouth, esophagus, and even internal organs.
Equipment damage: Hard metal particles can seriously wear or even jam expensive crushers, grinders, pumps and valves and other key equipment, causing unexpected downtime and high repair costs.
Reputation and legal risks: Once products containing metal foreign matter enter the market, they will inevitably lead to consumer complaints, large-scale recalls, serious damage to brand reputation, and even face severe regulatory penalties and lawsuits.
The above factors are the stage where magnetic separators come into play. They use the magnetic field generated by powerful permanent magnets (such as neodymium iron boron) or electromagnets to accurately "capture" ferromagnetic metals (iron, steel) and some weakly magnetic metals (such as some stainless steel) at key points in the food processing process. The working principle is that when food materials flow through or approach a strong magnetic field area, the ferromagnetic metal impurities in them will be firmly adsorbed on the surface of the magnet by the magnetic force, while the pure food passes smoothly, achieving precise separation.
What types of magnetic separation equipment are used in the food industry?
There are several types of magnetic separation equipment commonly used in the food processing industry, including:
Plate magnets: These flat magnetic plates are most commonly found in conveyors or chutes. They are often used to remove metal contaminants from dry goods such as grains, seeds or pet food.
Grid magnets: Similar to plate magnets, grid magnets are also suitable for dry material applications. These magnetic separators are composed of multiple magnetic bars through which the material passes. The magnetic bars collect and remove iron impurities from the material. Grid magnets are available in a variety of designs to suit a variety of material types, such as flour, grain, sugar, and more.
Rotary magnets: These magnets are most effective for dry, sticky, difficult-to-flow products that have bridging issues, such as milk powder or sugar.
In-line magnets: These types of magnetic separators include designs suitable for both dry and wet applications, as well as high-speed product lines, pump lines, and pneumatic conveying.
Magnetic separation technology ensures safety: not only equipment, but also a system
* Comply with regulations and standards: HACCP (Hazard Analysis and Critical Control Points) system, ISO 22000, FSSC 22000 and other global food safety standards all list metal foreign matter control as a critical control point (CCP) or prerequisite program (PRP). High-performance magnetic separators are the basic hardware to meet these requirements.
* Equipment selection and verification: The magnetic strength, form and installation location must be scientifically selected based on material characteristics (dry/wet, particle size, flow rate), expected metal size and type. Equipment performance needs to be verified regularly (such as using standard test pieces).
* Strict maintenance procedures: This is the lifeline to ensure the continued effectiveness of magnetic separation equipment! Must establish and implement:
* Regular cleaning: Clean the metal impurities adsorbed on the surface of the magnet according to the plan (such as every shift, every day) to prevent accumulation from causing magnetic field shielding or re-mixing of impurities.
* Regular inspection: Check whether the magnet is damaged, whether the coating is intact (to prevent food contamination), and whether the magnetic force is attenuated (regularly use a gauss meter to test).
* Records and traceability: Detailed records of cleaning, inspection, and metal impurities found to ensure the process is traceable.
In the field of food processing, magnetic materials and their separation technology are by no means dispensable supporting roles. They are the cornerstone of building a food safety defense line and the guardian of efficient operation of the production line. Intercepting every potentially harmful metal impurity from the source is a manifestation of the modern food industry's responsibility for consumer health and a wise investment for companies to achieve sustainable development and win market trust.
Therefore, please pay attention to these "invisible guardians":
* Scientifically select applicable magnetic separation equipment.
* Strictly implement maintenance and cleaning procedures.
* Deeply integrate it into your food safety management system.